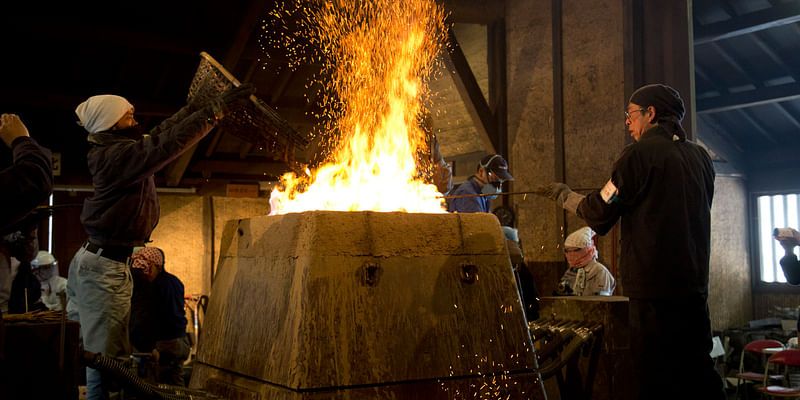
The crafting of Japanese swords, particularly through the traditional Tatara method, is a fascinating blend of art, science, and history, evoking a sense of awe and reverence. This ancient technique, practiced exclusively in the Shimane province of Japan, is more than just a method; it’s a legacy that has been meticulously preserved through centuries, making the katanas produced via this method not just weapons but revered artifacts that command prices as high as $105 million. The allure of these swords lies in their unparalleled quality, history, and the dedication to craftsmanship that goes into their making. This article aims to unfold the mystique of the Tatara method, exploring the journey of making the world-renowned Japanese samurai swords from the gathering of iron sand to the final, gleaming masterpiece.
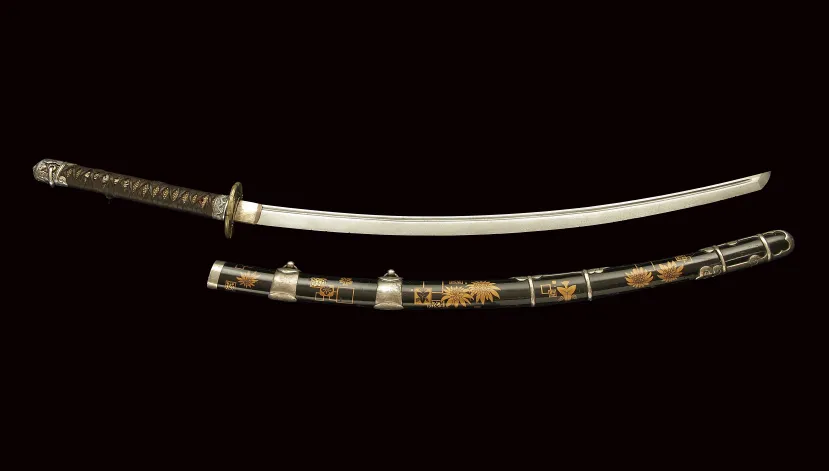
The Tatara Method: A Glimpse into the Past
At the heart of the Tatara method is the Tatara smelter, a structure that’s much more than a mere furnace; it’s a crucible where history, metallurgy, and craftsmanship converge. This method has remained unchanged for over 1300 years, a testament to the timeless techniques of Japanese swordsmiths. The smelter in Shimane province is particularly noteworthy, being lit for only one night each year in a ceremonial process that echoes back to the days of the samurai. This annual event is not just a process but a ritual, preserving the sanctity and tradition of sword-making.
From Sand to Steel: The Journey Begins
The journey begins not in a mine, but on the beaches of Shimane Prefecture. Here, beneath the whispering waves, lies the secret ingredient – iron sand. This isn’t your average playground sand, however. Rich in iron oxide, it’s the foundation for Tamahagane, literally translated as “jewel steel,” the heart of a katana. But not all iron sand is created equal. The sand in Shimane boasts a remarkably low level of impurities, particularly sulfur and phosphorus, which can make steel brittle. This inherent purity is a key factor that contributes to the exceptional quality of blades forged using the Tatara method.
The Science of Smelting: Unveiling the Mystery
Imagine a colossal, clay-built furnace, a testament to human ingenuity. This is the tatara, a behemoth that burns for only one night a year in Shimane. Layers of charcoal, iron sand, and a secret flux (a material that helps remove impurities) are meticulously stacked within. Bellows, traditionally operated by foot, roar to life, sending a torrent of air that ignites the charcoal, reaching temperatures exceeding 1,500°C (2,732°F). Throughout this fiery night, the iron sand undergoes a remarkable transformation. Lighter impurities rise to the surface as slag, while heavier molten iron sinks to the bottom. This molten iron isn’t homogenous, though. It separates into various grades depending on its carbon content. The highest quality steel, with just the right amount of carbon, is what swordsmiths prize most – a true testament to the masterful control achieved in this one-night spectacle.
Forging Legends: The Art of the Sword
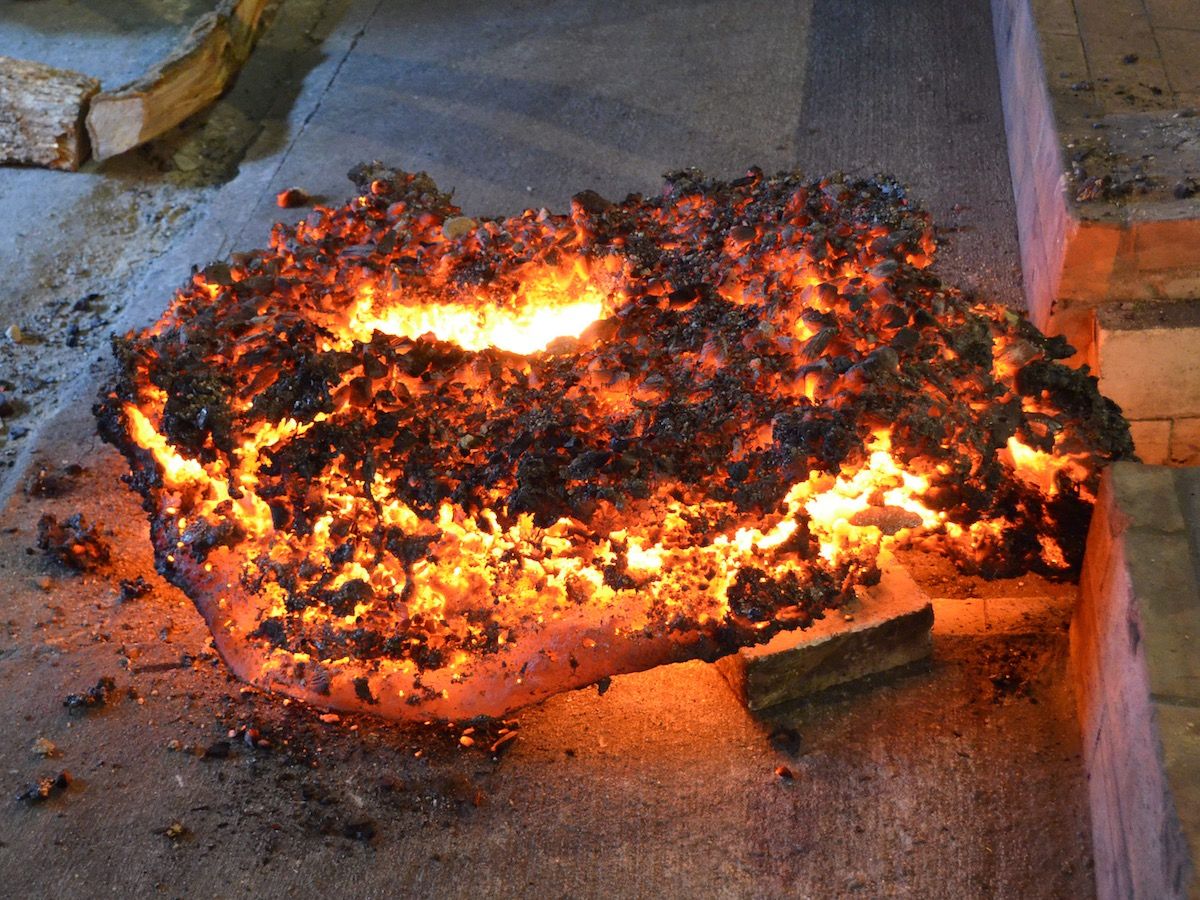
Once the Tamahagane is prepared, it embarks on the journey to become a katana. This process is as much an art as it is a science, involving careful heating, hammering, and folding of the steel. Each fold, meticulously carried out by the swordsmith, not only spreads impurities but also aligns the steel’s structure, enhancing its strength and flexibility. The swordsmith’s expertise in manipulating the metal’s temperature and shape is crucial in creating a blade that is a perfect balance of sharpness and durability.
Polishing the Masterpiece: A Reflection of the Soul
The final stage in the creation of a katana is polishing, a labor-intensive process that brings out the blade’s aesthetic and functional beauty. This painstaking task, performed by skilled artisans, highlights the unique patterns in the steel, revealing the sword’s “soul”. The polish not only enhances the sword’s appearance but also its cutting efficiency, making it a true masterpiece of craftsmanship.
The Legacy Continues
The Tatara method, with its roots deeply embedded in Japanese culture and history, continues to fascinate and inspire. It’s a reminder of a time when the sword was a symbol of honor and the soul of the samurai. The katanas forged through this ancient technique are not merely weapons but symbols of the relentless pursuit of perfection, embodying the spirit of dedication and excellence that defines the samurai ethos.
The reason Tatara-forged swords are held in such high regard and command astronomical prices is multifaceted. It’s not just the historical significance or the craftsmanship; it’s the enduring quality and the blade’s performance that set them apart. The unique combination of flexibility and hardness achieved through the Tatara method ensures that these swords are not only incredibly durable but also capable of an edge sharpness unmatched by any other steel.
The Tatara method is more than just a technique for making swords; it’s a living tradition that represents the pinnacle of Japanese craftsmanship. It encapsulates a blend of history, science, and art that transcends generations, producing swords that are not just tools of combat but revered works of art. As we delve into the world of Japanese sword making, we not only uncover the secrets of an ancient craft but also the spirit of the samurai, immortalised in steel.
Edited by Rahul Bansal