Designing new hardware products that have a positive impact on customers is no small feat. There are several elements that go into hardware product design that taps an unaddressed customer need, has the customer WOW factor, and succeeds long term in the market. Complicating the development of a useful product is the stringent safety and compliance approval testing that varies based on country and industry.
By: Kevin Bailey, CEO at Design 1st
Businesses have a lot to think about when they have a new product idea and one missed step in the product development lifecycle can significantly impact business success. It’s not just the hardware product design process and all of what this entails – from developing and testing a prototype, to engineering the mechanics, electronics and software, to setting the product up for manufacturing. One of the biggest hurdles – particularly with medical devices, baby products, and food safety products – is how to successfully navigate regulatory standards where potential user and environmental risks of new features must be carefully assessed and documented.
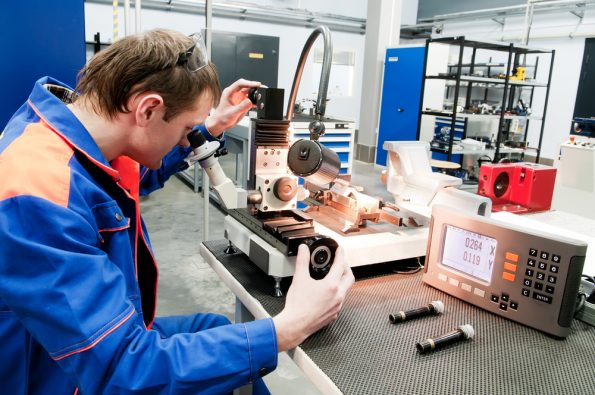
Worker in uniform checking quality of countersink reamer sharpening using precise optical device
There is no one-size-fits all product design strategy when it comes to regulatory compliance. Safety and regulatory standards are different for each market and there are variations you must consider for each Country. Here are best practice tips to consider to ensure your next hardware product doesn’t get delayed or worse lie dormant for years due to regulatory hold-ups.
1. Get familiar with ensuring safety and minimizing product interference.
With any hardware product design, there are no easy recipes for navigating regulatory requirements when you introduce new products and features in the market. However, you can and should get familiar with what you are up against by examining other comparable products in the countries where you plan to sell your product. Two primary concerns of regulation are the safety of the products to users and making sure the products you design do not interfere with other products currently operating in the market.
There are hundreds of test protocols and conditions to navigate and test labs are available to categorize products and applications to help guide you to the relevant approval requirements. Remember, regulatory and compliance requirements differ by industry. As an example, all major global markets regions require that electronic devices for sale in public markets meet radio emissions specifications (industry known as Electro-Magnetic Compatibility) regulations, which vary by region. Manufacturers must ensure their products meet the specified regional regulations and have scientifically traceable (i.e. certified test equipment and test environment) results available for governing agency review. In many cases the manufacturer must file the test data results with the relevant government authority.
Failure to meet regulations in advance of market sales can have serious business consequences including product recalls and border import shipment seizures. A conscientious development team will assess and test the required EMC risks well before product release and avoid correcting EMC issues late in the development lifecycle where cost of changes skyrockets.
2. Certification research for new parts.
You can take some of the compliance risk out early by researching safety and emissions certification details on any new parts and new to market component configurations, as you develop your new product concept. See if data exists early on in your component’s selection process suggesting poor safety and/or performance issues that indicate you should avoid using. With medical products there are additional tracking requirements during the design stages as your hardware product design concept evolves. As an example, by the end of the development up to 80 documents are required to be submitted for FDA approval of a class 1 or 2 medical device.
For system products that interact with the cloud or connect to smartphones the product must meet a defined varied set of regulatory requirements depending on class, country and product use location such as in a hospital or in your home. An example is at-home sleep apnea testing devices that monitor patient breathing patterns, and shares this personal data with other devices, which are also sent to cloud servers. It’s important to remember that data security and privacy, and patient safety while sleeping are controlled by regulatory groups for our benefit and require a set of tests associated with each known failure or risk.
3. Seek guidance from outside experts.
There are regulatory safety labs in large cities that can help if you know how these labs operate and how to ask for help for guidance long before you start the formal testing. These labs are ‘for profit’ centers and very expensive. I recommend finding a guide to help you in the early stages of your design while you are making important feature and part and product construction decisions. These decisions are critical as they determine your downstream quality management costs, regulatory approval testing costs and direct product assembly costs that last the entire life of the product.
A partner to help you navigate early-stage hardware product design and a test lab to provide their input as you finalize a design is the best scenario. Knowing what you are doing and having a good working relationship with the test house is critical if you do not want to repeat very expensive tests over and over again. Regulatory testing costs can be as much as your entire design development costs and more when you make mistakes.
4. Focus on part selection and product level planning early.
Your product has hundreds of technical parts, and the overall product assembly has its own specifications to meet. Each part typically has a performance spec sheet and in some cases a safety data sheet and a materials data sheet. This is the starting point for the person on your team in charge of regulatory approvals. If your product has 200 parts, then there are more than 200 spec sheets to get familiar with and organize for the submission. Experienced designers and engineers know most of the commonly used parts and their specs well. There will be a few parts, typically custom, that are new to your design team or new to the market and this is where you should focus.
Next is the product level planning. Regulatory testing labs test the product assembly, not just the parts, to meet the product category test pass or fail levels necessary to be approved for the Country and market you are selling in. Complicating things is that most regulatory tests you have to submit with your product have fixed test pass-fail limits but some have variable limits that you decide and your decision limits what you get approved for. Experienced guides know where the risks are, where to focus, when to get test lab experts to review the product, and the other intricacies of the formal testing process. Get a design expert to guide you and a test submission guide to reduce your time and development costs as you prepare, submit and achieve your approvals.
Remember, although there are regulatory and compliance risks that must be assessed for your new product idea, the hardware product design process can be highly predictable with a good guide. It should not deter you from making your great idea a reality and delivering a product that delivers new value and succeeds in the market.
The post Understanding the Regulatory Process throughout your next Hardware Product Design appeared first on The Startup Magazine.